What is lead time?
Lead time is the amount of time that passes from the point a process starts to the point it is completed. The term can take different meanings depending on the context. You can find the types of lead time below.
The term, ‘lead time’, is used in a number of different fields. These include manufacturing, supply chain management, supplier management, project management, enterprise requirement planning, material requirement planning and software development among others. Based on the way operations proceed, the exact definition of lead time would differ across industries. However, the basic definition is as given above.
To understand this difference across areas, consider the process of developing a new product, here lead time is the amount of time taken for a product to be released into the market. Similarly, in Supply chain management, it is the time from when the order is placed to when the customer receives the product. In software development, it’s the time from when a requirement is identified to when it is fulfilled.
If the lead time is lower, this is better for a company. It shows that the company is able to adapt fast to changing needs. Customers are also more likely to be satisfied when the lead time is lower. Shorter lead times are very important in efficient inventory management. So, whichever business you are in, you’d want to focus on lead time and work on improving it. Below, we’ve explained what are the factors that lead time depends on, how to calculate it, the types of lead time as well as general ideas on reducing this metric.
Calculation of lead time
The formula for calculating lead time would differ slightly from industry to industry. However, the basic idea is to include all the various places time gets used up in the process. So, you’d have to account for all these various factors. In general, your lead time formula would look something like this:
Total Lead Time = Pre-processing Time + Processing time + Waiting time + Transportation time + Storage time + Inspection time.
Here, a number of factors right from the preprocessing stage to the quality checking stage have been taken into consideration. Here’s what these components include:
- Pre-processing time - this is all the time that is consumed in receiving the order, ie, before you actually start preparing the product. The time in receiving, understanding and creating the order is taken into account.
- Processing time - the time that is consumed in either producing the product or procuring it.
- Waiting time - all the time while you are waiting in the queue for the product to be finished
- Transportation time - as is obvious, this is the time taken in transporting the product
- Storage time - the time when the item is stored in the warehouse
- Inspection time - time taken for quality testing.
In these calculations, it is assumed that there is no work currently in progress/ zero inventory.
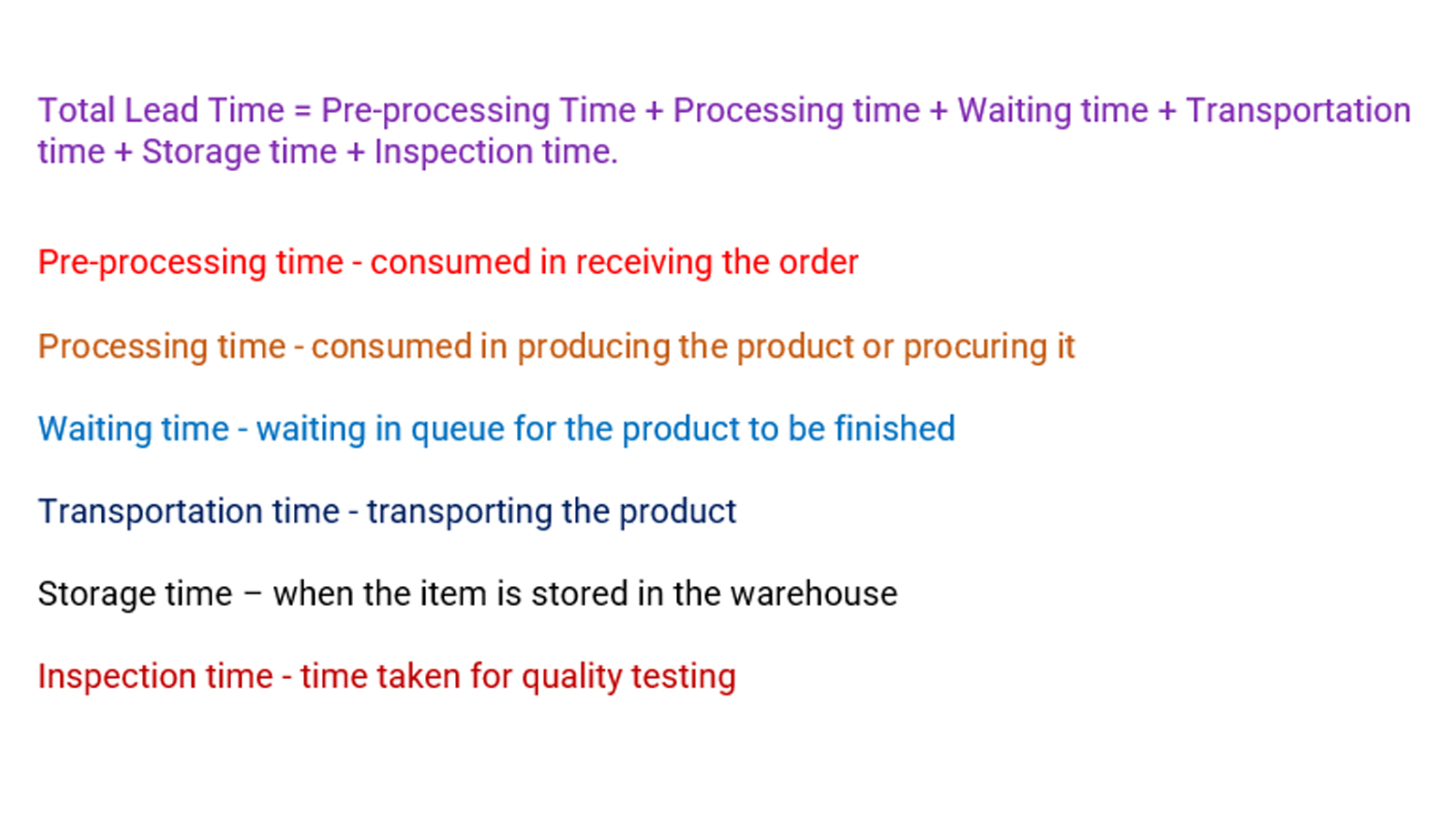
Types
As already mentioned, the types would differ depending on industry. In a manufacturing business, here are the four primary types of lead time.
Customer Lead Time
This is the time taken to fulfill customer’s orders. Basically, the time from when an order is confirmed to the point it is fulfilled. This fulfillment could be a pickup or a delivery depending on what has already been agreed upon.
Material Lead Time
Simply, the time to procure materials from the supplier. It’s the time from when you place an order with the supplier to when you have the goods in-hand.
Factory/Production Lead Time
When all the required raw materials are available, the amount of time that the manufacturer takes to prepare the final product is known as the production lead time.
Cumulative Lead Time
This is the sum of the material time and factory time. It is the amount of time passed from the point an order is confirmed to when it is delivered to the customer, including the procurement of raw materials and the subassembly of related units.
Factors affecting lead time
A number of factors, both internal and external, affect the lead time of a process. They could lead to an increase in this time or a reduction in it, depending on their behavior. Internal factors, like the ability of your business to process orders and deliver them are controllable. External factors on the other hand, such as how long your supplier takes to deliver the materials you need to use, cannot be effectively controlled.
Generally, the lead time can be divided into the following areas:
- The production processes a company employs. If you do something on-site, then there will be time losses in transportation and component delivery.
- How efficiently the inventory at the company is managed. A smooth production process is assured when the inventory is well-maintained. If the inventory management process isn’t proper, and the company falls short of some stock, then the entire process is held up which increases the lead time.
- The supply chain. Since estimating how much time the suppliers would take to deliver is tough, it gets tough to coordinate production. At the same time, stocking up on access to avoid this time loss would raise cost and maybe even lead to wastage.
Apart from these, there may be very specific factors in your industry. So now that we know what are the various factors, is there anything that can be done to improve it? Let’s find out.
How to reduce lead time?
The following are things you can do to reduce the lead time of a process:
Eradicate activities which do not add value to the process
Identify the activities that aren’t really adding value to the process by analyzing the process in detail. Then, work on removing or reducing such activities.
Change suppliers, keep a tab
Get info on a number of suppliers and score them based on your requirement. Your supplier is a key part of the process so you need to maintain a good relationship with them. Keep a tab on the activities and treat them like a part of the process. Make them realise the value of the function and give regular feedback.
Switch up transportation methods
With improving infrastructure, there might be an alternative mode of transport which is more efficient. Keep a track of this and make changes if possible. Equipment and employees should be available when needed.
Source raw materials locally if possible
If you get raw materials of an equal or better quality to what you have, locally, then you should consider changing suppliers. Since the transportation is over shorter distances when you source locally, this reduces lead time.
Reorder often
A lot of time may be spent waiting for the goods to arrive, and this is common when you order in bulk. Instead, go for shorter batches that you ship frequently.
Standardize operations
If you have standard operational procedures, there will be little room for confusion among your staff members and this will lead to a shorter lead time. Hence, make sure everything is clearly documented and easily accessible at all times. This also minimizes human error.
Automate the process
Building on the above, when there are automations in place, there is a reduced need for human intervention. This means that there would be an improved lead time and faster delivery. So, try to find ways of automating the process wherever possible.
Maintenance
Avoid all unnecessary downtimes by frequently having planned maintenance of any machinery that you make use of.
Examples of Lead Time
Consider a small soft drink manufacturer which has to supply a hundred boxes of 120 one-liter bottles each to a customer on a certain date for an event.
Suppose the company takes about 30 minutes to finalize the order; 16 hours to package the boxes, split into time for making and mixing the syrup, quality testing, blowing and filling bottles, and packaging them into boxes. Another 36 hours would be consumed in shipping the crates to the event location.
Combining all of this, the total lead time would be 52.5 hours.