What is the Product Process Matrix?
The Product Process Matrix (PPM) is a matrix used to visually represent the relationship between the product development process and the process lifecycle. Product development process consists of all the steps from the ideation stage to the product’s growth or decline. Process lifecycle aims to achieve a more cost effective, standard structure. The matrix merges these two components together.
In production systems, the products usually vary in type and complexity. You can find both, custom made limited edition/low volume products as well as mass produced commodities. The Product Process Matrix tries to show how some production processes are better for certain product-volume mixes and others aren’t.
The matrix is two dimensional and illustrates the link between the product that is produced and the production process employed. One dimension describes the product structure/life cycle and the other describes the structure/life cycle of the process. Combined, these dimensions help an organization determine which approach is most appropriate for production of a product.
Origin of the Product Process Matrix
The Product Process Matrix, also known as the Hayes-Wheelwright Matrix, was first developed by Robert H. Hayes and Steven C. Wheelwright in 1979. They introduced the idea in articles in the Harvard Business Review, titled, ‘Link Manufacturing Process and Product Life Cycles’ and ‘The Dynamics of Process-Product Life Cycles.’
These two articles explored issues in market manufacturing processes and attempted to make use of the matrix to come up with strategic solutions. This gave organizations a tool to estimate the progress of a product along with related processes and to analyze the fit.
Understanding the Product Process Matrix
The matrix
As already mentioned, the PPM matrix is two-dimensional in nature. It is split into columns and rows representing the product and process life cycle and structure.
The columns show the types of products split into the following categories:
- Low volume products which are one of a kind, have a low standardization
- Multiple products, not one-of-a-kind, but having a low volume
- Few major products which have a higher volume.
- Commodity products which have a high volume as well as high standardization
The rows of the matrix show the process choices as follows:
- Jumbled flow
- Disconnected line flow
- Connected line flow
- Continuous flow
You can see this represented in the below image.
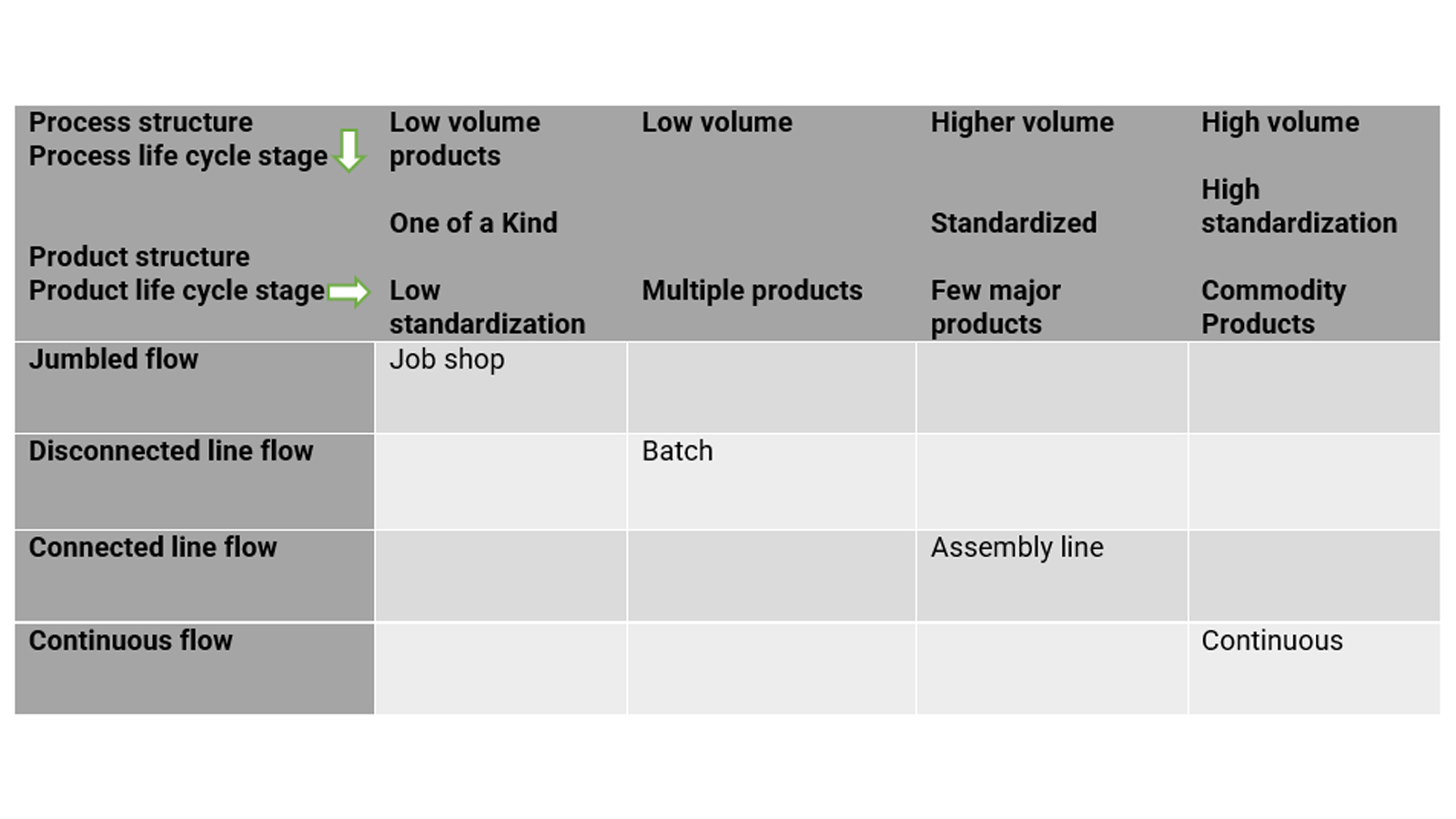
Hayes and Wheelwright determined that most organizations fall along the diagonal of the matrix. In this area, the product and process choices logically align with one another.
In this matrix shown, there are four distinct stages outlined. In the first stage, the production process isn’t standardized and this results in a higher cost of production. But, by the fourth stage of the matrix, there is standardized, mechanized, automated, and highly effective production.
Let’s understand these four stages in detail in the further sections.
Job shop
Organizations in the job shop stage usually produce a number of varied products in comparatively low volumes of production. Due to this low volume, there is the chance of a lot of flexibility in the workers as well as the equipment being made use of.
The products in this stage are unique/one of a kind items which are heavy on the amount of customization involved. Direct interaction with the customers who buy these products as well as a highly skilled set of workers is involved in this type of production.
This type of process, although it involves a good amount of creativity and flexibility, has little to no repetition involved. Inevitably, this often leads to inefficient and time consuming production if the proper material and skills aren’t easily available.
Batch production
In the batch type of production, the number of goods produced is more than in a job shop. However, the volume of production per good is not high enough to justify the need for equipment dedicated to its production.
The efficiency of this type is a bit more than a job shop since there is grouping of parts in processes as required. Note that it’s still at a low volume. The repetition in the process is good for creating a smoother flow, but it’s not a continuous connected process.
Assembly Line
In the assembly line process, products which are very similar to each other are produced in a repetitive way. Products pass in a sequential order in workstations that have been set up for their production. This results in an improved efficiency of the process.
Since the process is standardized, it is much easier to manage and oversee the process. The product, however, has next to zero flexibility or variety. The company is enabled to produce goods in high volume at a quicker pace, though.
Continuous flow
As the term itself suggests, this process takes place in a continuous manner. For this, specialized equipment is made use of. To make this efficient and justify the costs of the special equipment, the range of production would have to be very limited and the volume of production would have to be very high.
However, when these two conditions are met, this process proves to be the most efficient type of production as the process is highly standardized. Maintaining the standard of production across products is very easy in this case.
Of course, there is zero flexibility in the process and customization of the product isn’t possible. In the event that there is any damage to the equipment, too, it results in a lot of downtime and production gaps. There is also the added cost of repairing the equipment.
Off the diagonal line
Some companies may choose methods of production and processes that do not come in the diagonal area of the matrix like the above four. This is preferred due to the competitive advantage offered by such products for a company. Although this works out well for some companies, others who make the shift without understanding implications could be putting themselves into trouble. This is due to the heavy costs and risks of being different from the competitors that are involved.